Why Candy Brands Choose Hard Candy Machine Technology
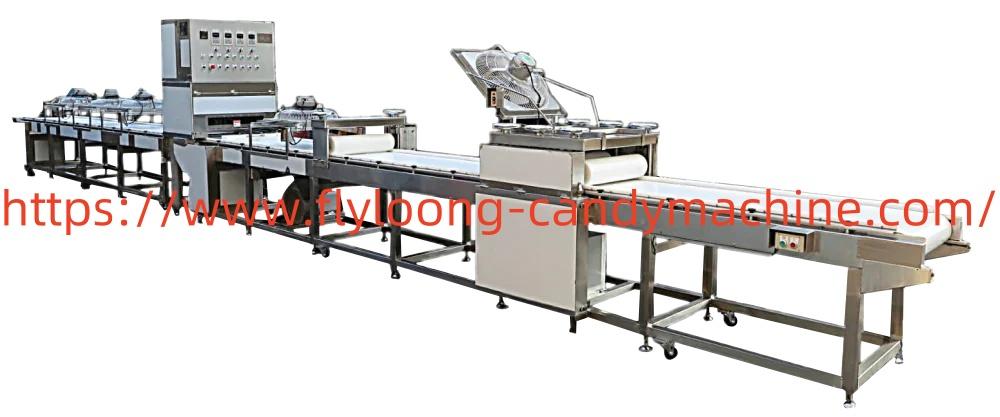
In the evolving confectionery industry, the hard candy machine remains a central tool in improving both production efficiency and candy consistency for manufacturers aiming to meet modern market demands.
One of the most valuable advantages of using this type of machine is its ability to streamline the candy-making process. Traditionally, hard candy required manual pouring, shaping, and cooling steps that involved significant labor and time. With automated molding systems, the modern candy-forming process has become far more reliable, reducing material waste and ensuring consistent shape and size across all batches. The FLD350 model, for instance, provides precise control over the heating and depositing stages, resulting in higher-quality finished products.
Temperature control is one of the key elements in hard candy production. Without accurate heating, the sugar mixture might crystallize or fail to reach the proper consistency. A well-engineered machine regulates this with electronic precision, supporting even large-scale production without quality loss. Furthermore, molds can be adjusted for custom shapes, making it easier for producers to adapt their offerings for seasonal or branded promotions.
Hygiene and food safety are also critical factors. Stainless steel construction in modern candy machines minimizes contamination risks and simplifies the cleaning process. This is especially important in the food industry, where regulatory compliance is non-negotiable. The FLD350 and similar equipment models often include automated lubrication and easy-access compartments to facilitate routine maintenance.
For candy producers seeking to diversify their product lines, these machines also allow quick adjustments. Manufacturers can change the candy's color, flavor, or even insert fillings like powdered sugar or fruit gel without overhauling the entire line. Such flexibility not only saves time but also supports market responsiveness, a vital edge in today's competitive confectionery landscape.
Moreover, energy efficiency is becoming increasingly important in the global push for sustainable manufacturing. Machines like the FLD350 are designed to operate with reduced energy consumption compared to older systems, lowering both environmental impact and operating costs. These savings accumulate significantly over time for medium- and large-scale facilities.
From a business perspective, investment in automated candy machines contributes to long-term productivity. Reduced labor requirements, minimized human error, and maximized output all enhance return on investment. In many cases, smaller confectionery brands can scale up thanks to dependable machinery, allowing them to meet growing demand without sacrificing product integrity.
In conclusion, for any enterprise in the sweet-making sector, adopting advanced candy-forming technology is a strategic step toward modernizing production. The shift not only delivers tangible operational benefits but also improves the overall product appeal, making a brand stand out in an increasingly crowded marketplace.
To explore more about automated candy solutions, visit www.flyloong-candymachine.com.